In 1995, “Mutant Materials in Contemporary Design” introduced Paola Antonelli to visitors of New York City‘s Museum of Modern Art. Formerly a lecturer at the University of California, Los Angeles (1991 –1993), she joined MoMA‘s Department of Architecture and Design in 1994 as associate curator. Proclaiming, “Today, adherence to the ‘truth’ of a material is no longer an absolute for design,” “Mutant Materials” displayed uses for materials that transformed their physical characteristics as well as their capabilities. Although Antonelli has gone on to curate several equally successful exhibits, such as last year’s “Workspheres,” “Mutant Materials” qualifies as her favorite. David Sokol caught up with her to discuss the exhibition’s continued relevance, as well as recent innovations in material development and applications.
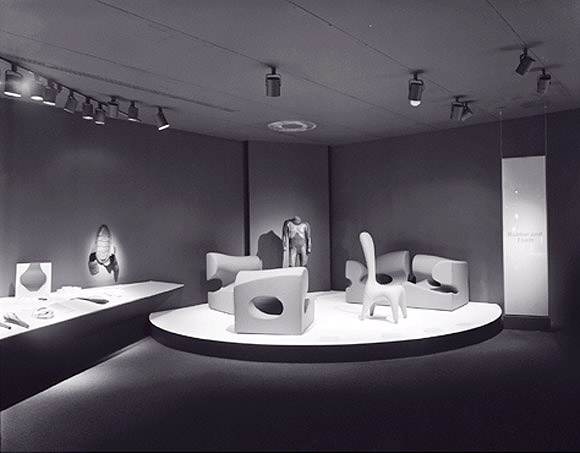
David Sokol: I’ve read that “Mutant Materials in Contemporary Design” was your favorite exhibition to curate. Why is that?
Paola Antonelli: It was my first one at MoMA, and it was a completely new way of doing exhibitions for me. I had done a lot of exhibitions before, but never to preach to a very wide public. Design is really a shared cultural component, but in the United States it’s much less recognized than in Europe. It was great—I was trying to address a very large public and at the same time educate, entertain, and add a little piece of scholarship to the work done on materials.
DS: And did the public respond in kind?
PA: Oh my god, yes. About 80% of the objects were touchable. And the tables were low enough that children could touch them. It had about 400,000 visitors, and so the public success was very strong, and the success with the design community was very strong.
DS: Why do people love to touch?
PA: The intellect is never enough. You have to engage the other senses. Sight is not enough. Sight is the first and always-respected sense. Touch is normally the forbidden fruit, so, when you give it to people, not only can they complete the experience, you give them a new freedom that they hadn’t experienced before.
DS: A lot has changed since 1995—the Internet exploded, for instance, and we’re still trying to understand the economic and cultural ramifications of that. Have these phenomena affected the evolution of materials research and applications?
PA: No, I don’t think so. There has been progress in general. What the exhibition was trying to capture was a curve, a moment of change in the use of materials. It was only the beginning. I’m saying quite immodestly, recent sea changes have underscored the exhibit’s relevance.
It was about this new, contemporary way to use materials. You can manipulate them, you can intervene in them as a designer—you don’t have to go back into the chemical lab. As a designer, you can actually do your work on them directly. You can bypass a lot, and that’s happening even more now. And so the exhibition—the assumption of the exhibition—is still valid. And I think it will be valid for quite a long time, and direct intervention will only increase.
DS: Has a material that was innovative in 1995 now experienced widespread adoption?
PA: The ones that are persistently out of designers’ reach are metals, of course. But there are many more resins that can be mixed under circumstances that are within reach. Many composites are made by big companies, but you can also mix fibers with resins and actually make them yourself. If you’re thinking of Kevlar, if you’re thinking of fiberglass, they are fibers—of carbon, of glass—and those fibers and resin are put in place. You act sculpturally at the beginning. If you have to do the hull of a new vessel, for example, you can do it by hand.
Another big revolution has been in computer-aided manufacturing. Karim Rashid has done a lot of experimentation with Nambé (the Santa Fe-based manufacturer of art objects for the home and office). The etching patterns for the Morphe crystal line were generated by computers that were giving instructions in a random way. In this instance, the patterns were actually applied by hand, but ultimately you can have a series in which every piece is different, yet you won’t have to stop the machine and lose production. It is the dream of the diversified series first introduced in the ‘80s.
DS: So who’s working with what now?
PA: Rashid is one, definitely. Also Ross Lovegrove in England and Alberto Meda in Italy. These are the ones that have been really specialized in testing out new materials. There are big companies like IDEO that have a lot of access, and then you know that there are new services like Material ConneXion that have tried to spread these new riches among companies and designers. If you go to their headquarters and look at the samples of the materials, it’s mind-boggling.
DS: In addition to Meda, are there any other architects who come to mind?
PA: Toshiko Mori, AIA,—she’s very, very focused on materials. One of the most public applications of materials she’s done, which everybody loved, was Pleats Please for the Issey Miyake store. But I would say that pretty much all architects I know are working on materials. It makes sense. Gaetano Pesce was trying to do a whole house in plastic.
You must not forget the interiors. Another person who uses an amazing array of materials in a dynamic way is David Rockwell. I just went to the Mohegan Sun Casino Resort, which he designed, and the kinds of materials he used, like turkey feathers encased in glass, onyx fused onto glass, and woven birch bark, are too many to count.
But it’s almost unfair to talk about a few designers, because so many do experimentation. The ones that I mentioned to you are renowned for testing new materials by doing new products with companies. There’s a company, for instance, that does work with fabrics, called Edra. They have plastic slipcovers, they’re soft as silk. And inside, there’s hay. It’s not only about advanced materials; that’s the beauty.
DS: What, then, makes a material mutant? What makes it contemporary?
PA: The idea came from maintaining personality while being able to change form and performance, a little bit like the mutants in science fiction movies. Once, if you played mental association with somebody, and you said “ceramics,” and the person said “teacup,” the person would be completely right and exhausting the possibilities for ceramics. Now, if you say ceramics, and somebody tells you teacup, it’s an association that doesn’t begin to describe what ceramics are today. You have a razor blade, and the ceramic looks almost translucent. For rotors, it looks like metal. It’s the same material, but the applications and performances are so different and diverse.
There are trends in materials that you’d call contemporary simply because they have elicited a fascination from contemporary designers, and some of them are mutant, and some of them are not. I think ‘contemporary’ is a pretty superficial label. I don’t know if it would mean that much to me as a category. For a while, it was titanium, so ‘contemporary’ means nothing more than those things that you can see as being hailed and used a lot.
DS: Is there a “green” component to the definition of mutant?
PA: There’s no component of green to the word mutant. In the exhibition, I purposely did not have a section devoted to green materials. I presume that any responsible designer or manufacturer is going in that direction. Also, sometimes, green materials have an invisible greenness—such as efficiencies in production, or longevity—and are not just recyclable. There’s much more to the idea of greenness. It’s about sustainability. So I tried to include objects that were long lasting in nature or had responsibility designed into them, but without singling them out.
DS: So that doesn’t mean that, say, only natural materials are responsible?
PA: Right. I am so tired of the simplistic ideology that so many people apply to greenness. I really respect the work of William McDonough, FAIA, because he’s actually tried to work within the system. He’s trying to teach people to be sustainable by acting on all the different components of the production process, as opposed to switching from plastic to wood. So it really takes so much more than natural materials to be able to have an impact on the current pollution and consumption of the environment. It’s crazy to think that you can stop factories from producing, and the consequences of that would be unemployment and, in the end, even more damage to the environment. It’s something I take very seriously, but it’s something I don’t like to preach about.
DS: How are materials studied? Is the architecture firm that studies materials differently structured from one that doesn’t?
PA: I really don’t know. I don’t think it’s necessary. You might have somebody on staff who is really passionate about it and wants to study it. You might have a subscription to Material ConneXion, and so you might go there. You might live near the Jet Propulsion Laboratory in Pasadena. You might live in Connecticut, and you might be close to a sailboat company that uses a lot of carbon fiber. It starts with passion and interest first, and then you adapt your tool.
But I believe that you can be in New York and do things only with wood, and you can be in Kansas and be obsessed with high-tech materials. Ultimately, I don’t think it has anything to do with geography or access.
DS: How and with whom can architects get more involved with investigations into innovative materials?
PA: I have a refrain that all of the most advanced materials get tested by militaries and by surfers. And afterwards they get down to normal people. The sports and military fields are really where most materials are tested, because they’re looking to minimize the use of energy and maximize performance. With the military, there were, at the time of the exhibition, five technology transfer centers in the U.S., and you call them up to find out if materials used in war or military purposes were now available for civilian uses. (For further information on military products, contact the public relations department of the U.S. Materiel Command, Alexandria, VA (703) 617-8010.)
DS: Techniques are becoming more widespread, materials are becoming more accessible. What’s next?
PA: If you simplify the conditions for manipulating materials so that it can be done at ambient temperature and ambient pressure, and you reduce the toxicity, then there you go. It’s also ceramics, it’s also wood—it really depends on the ingenuity and creativity of the designer and architect.
There is a recouping of craftsmanship in the world of industrial design, so a lot of contemporary design now takes into account handiwork. And, it puts back an artistic spin on work that is almost engineering. It’s still the goal to achieve an industrial process, but it’s easier to experiment—so you can be able to prototype without having to invest $50,000. I think this is a great moment for design.
Interviewer David Sokol is a New York-based writer who regularly contributes to Architectural Record and Metropolis magazines; he has also written for Oculus, Architecture, and Grid. Currently, Sokol is an associate editor at Shopping Center World, a real estate and retail design trade magazine.
Opening photo illustration by Supreeya Pongkasem.
Originally published 4th quarter 2002, in arcCA 02.4, “New Material.”