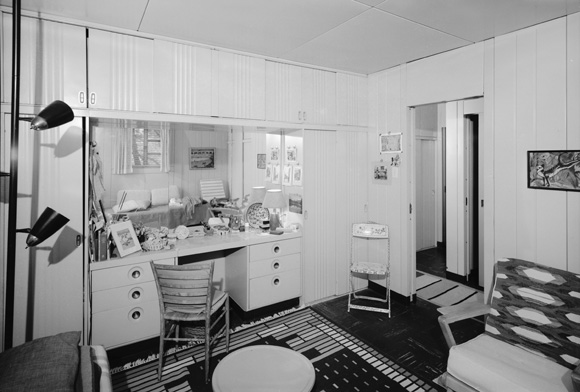
Architects have historically embraced the cause of residential prefabrication with vigor, designing a wide variety of futuristic “concept” homes intended for mass production. Among elite examples are Buckminster Fuller’s “Dymaxion” house (1929-46), Albert Frey and Laurence Kocher’s “Aluminaire” house (1931), and Walter Gropius and Konrad Wachsmann’s package prototypes (1941-50). All reflect the conviction that prefabrication can be fundamental to the production of single family housing, although none reached the mass market in any significant quantities.
Modern architects’ longstanding affair with prefabrication serves as a useful backdrop for an interesting and mostly forgotten example, the “Lustron Home” (1947-50). This brief but significant building experiment resulted in the construction of nearly 2,500 units throughout the Midwest and Eastern Seaboard.
The modest Lustron Home was an unlikely protagonist in the century-spanning exploration of the idea of prefabrication. It was also a cultural by-product of innocent, Popular Mechanics-inspired notions of the future and the enthusiasm generated by wartime mass-production success. Promotional literature promised low maintenance costs, since all interior and exterior surfaces—including the roof—were constructed of porcelain enamel panels. The original, 31′ x 35′ (990 square foot) two bedroom house was priced at an affordable $7,000 and included built-in fixtures throughout. Among these fixtures were a combined clothes and dishwasher, lighting and bathroom fixtures, automatic water heater, exhaust fans, plumbing, electrical equipment, a 275 gallon water heater, and radiant ceiling heating. The steel in each unit weighed 12.5 tons; the enamel weighed a ton. All 3,000 parts could be shipped from the factory in Columbus, Ohio, in a single, 35-foot tandem trailer and be site-assembled in 350 hours. Land costs were not included, and local dealers were set up to assist with customer orders and lot selection.
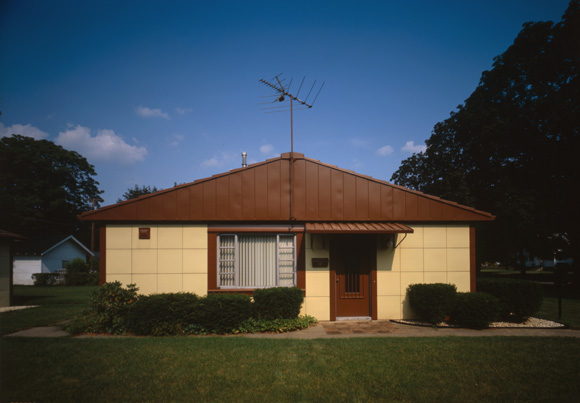
By the end of the company’s short existence in May 1950 it had constructed a total of 2,489 houses, with a significant number of remaining back orders. While never reaching its break-even production rate of 35 houses per day (much less its projected rate of 400), in July 1949 it reached a peak production rate of 15 houses per day. When the company repeatedly failed to reach its predictions and required significant additional loans, bankruptcy followed.
Mass production efforts of private companies had played an important part in helping to win World War II. With such successes in mind, the U.S. government poured $37.5 million in loans into the Lustron Corporation. The company was the outgrowth of a Chicago firm whose decision to produce prefabricated houses was born out of a frustration with the lack of postwar steel for the company’s principal product—porcelain enamel metal panels for gas stations—and the government’s offer of support for firms that would address the serious shortage of housing for re turning G.l.s.
While it lacked the visionary pizzazz of Buckminster Fuller’s prototype, the Lustron Home reached the markets in numbers that few other experiments in prefabrication ever would. By the end of 1949, its distribution network included 234 dealers in 35 states, reaching from New York to Florida and South Carolina to Texas. North Carolina received the most houses (339), while Illinois (307), Ohio (275), and Indiana (142) were leaders. Even North Dakota (12) and Florida (16) were represented. Not surprisingly, a large number of Lustron Homes still exists. Current owners’ documentation of repair strategies, original sales information, and other historical details recall the impact of the experiment. They also remind us of the Lustron’s strange mix of visionary and pragmatic influences and the dream of a technologically advanced domicile for a new and better world.
Author David Thurman, AlA, LEED AP is an Associate Partner at Zimmer Gunsul Frasca Architects LLP in Los Angeles. This article is excerpted from a full-length article in arcCA 02.3, “Building Value.”
Originally published 4th quarter 2007 in arcCA 07.4, “preFABiana.”